A public charging or fleet charging site—or pretty much any installation larger than one or two Level 2 chargers—consists of more than just the chargers that drivers interact with. There’s going to be a transformer, a cabinet full of switchgear, and increasingly, microgrid elements such as battery storage and/or PV panels.
ABB makes all kinds of switchgear and other commercial electrical gadgets. At the recent Daytona 500 race, Charged spoke with Amber Putignano, Market Development Leader for ABB E-mobility, and we asked her how the interaction among the various electrical components might affect reliability. She shared some insights on how to make a charging site more reliable and more future-proof, and also outlined a developing trend in the industry—controlling functions, now often performed within a charging station or in the cloud, are increasingly migrating to the switchgear level.
Today, at most sites, there’s not really any software integration between the charger and the electrical equipment behind it.
“The reliability problems, at least that I hear about, tend to be more specific to chargers,” Ms. Putignano told me. “In general it seems to be the connection between either the charger and the vehicle or the charger and the back-end payment system. But the electrical gear that is behind all of that is often not connected in any way other than by power. Today, at most sites, there’s not really any software integration between the charger and the electrical equipment behind it.”
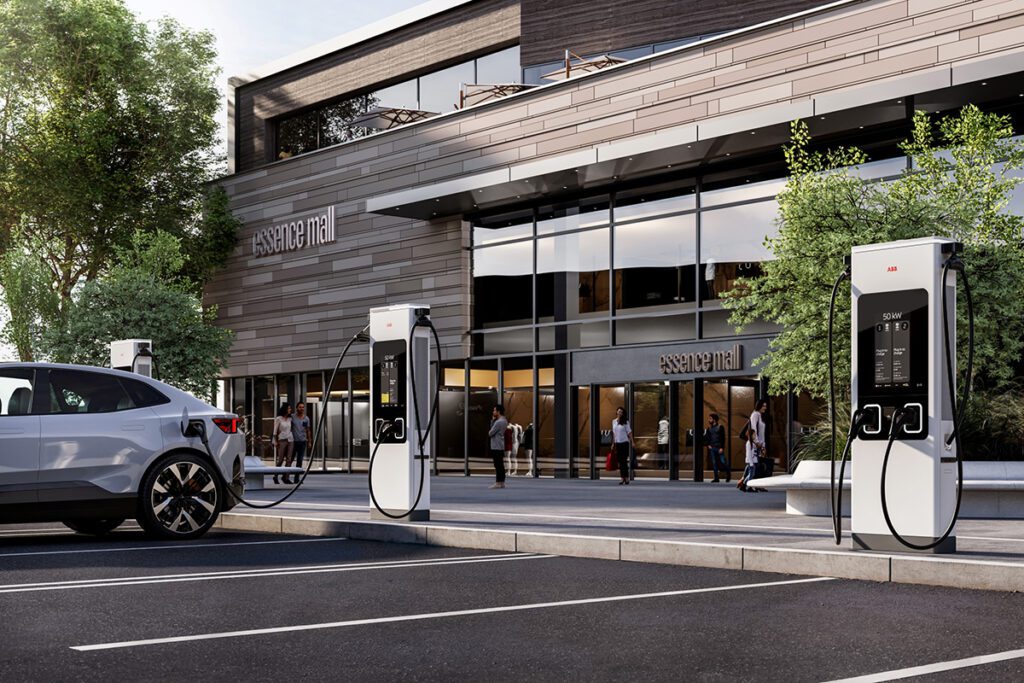
For various reasons (obsolescence, newer technology, companies going belly-up), chargers themselves tend to be replaced fairly often, but that’s not necessarily the case for the switchgear and other ancillary equipment. “The equipment that goes behind the charger is designed to last 20 or 30 years, whereas chargers are designed to last 10 years, and over time technology is changing, companies are moving in and out,” Putignano explained. “As the segment evolves, I think we’ll start to see some of the functionality that today happens at the charger level, move to that equipment level behind the chargers. For example, if you are using an energy management system that’s based on a cloud system [tied to] the charger, and down the road you need to change the charger or that company doesn’t exist, you have a system that may not work for the next generation of chargers. So I think there are opportunities for companies to move that functionality back to the electrical equipment, which is going to have a longer life and be more charger-agnostic, so the operator doesn’t need to be as concerned about whether their energy management system is going to work with new technology.”
So, are we going to see chargers becoming dumber, as the smarts move to the switchgear? Putignano thinks that’s a likely scenario. As microgrids become more prevalent, charging, solar generation and battery storage all need to be coordinated, and that’s not a job for an individual charging station. “All of that control should happen at a higher level in the system, such as the switchboard. People will probably learn the hard way that charger-agnostic solutions are the way to go.”
A lot of the energy management that’s available today is on the cloud level, but I think it’s going to move more on-site as you start integrating battery energy storage and solar, and also as EV batteries evolve to take more power.
Over the past few years, it’s become hip to run everything in the cloud, but there are a couple of good reasons why charging sites should be controlled by a local processor instead.
“A lot of the energy management that’s available today is on the cloud level, but I think it’s going to move more on-site as you start integrating battery energy storage and solar, and also as EV batteries evolve to take more power,” Putignano told me. “If you think of an electric truck plugging in and out, that’s a significant amount of power on and off, and you want the system to respond very quickly. Cloud-based systems have a longer response time, and they’re reliant in many cases on a broadband connection.”
Of course, it’s not unheard of for an internet connection to be a point of failure, so when you consider response time, reliability and the need to be charger-agnostic, it would seem that the best place for the controlling computing power is at the switchgear level.
“If you’re looking at a site that’s focused on electric trucking, I think they’re really going to need that on-site, very secure, very vast reaction time from a system that’s also capable of pulling in solar, battery storage or whatever other assets they might have on the site.”
Ms. Putignano told me about a new standard that’s coming out: UL 3141 is going to define a type of energy management system that also provides protection against excessive current draw. “Typically, in the past, an energy management system’s main function was to control costs, provide peak shaving, level out your use of energy from the utility, perhaps with battery energy storage. In this new UL standard, they’re taking an energy management system a step further—it’s also required to protect the system.”
It’s not uncommon for a site to have a potential load greater than the amount of power available from the utility interconnect. Putignano explains: “Operators want to have as many connectors on a site as possible. Say a site has 10 megawatts worth of maximum power [draw] from the chargers, but they’re not getting 10 megawatts from the utility. Very rarely are all the vehicles plugging in at the same time with a low state of charge, so it’s unlikely that you’ll have all of those chargers running at full power at the same time. Therefore, it’s possible to have more chargers than power at the site. However, then they need to ensure that the site is protected and that they’re not exceeding the power available from the utility at any point.
“So, this new UL standard takes energy management a step further to require the system to do one additional function, which is protect the system. It’s not focused just on cost management or energy efficiency. It’s also protecting the system from overload.
“That standard’s supposed to be out this year. I think that, once this is available, this makes it even more [feasible] for these energy management and power control systems to exist in the switchboard, because there’ll be a standard that defines the function of how that system should work, and people will feel comfortable choosing it.”
Are all these functions available in a product that you can buy from ABB right now? “They’re actually two separate offerings,” Putignano explains. “We have the switchboard part, which is the breakers and the electrical distribution, and then you can complement that with a microgrid control system, which we’re working on to [comply with] that standard specification.”
Source: ABB E-Mobility